Mezzanine floor systems are a practical solution for businesses looking to expand their space without the high costs of building extensions. They can be easily adapted for use in warehouses, factories, and commercial settings to add extra storage or office space. However, installing these systems can come with its own set of challenges. In this article, we explore common obstacles for mezzanine floor installation and provide solutions to tackle them effectively.
Understanding the Common Challenges
Structural Integrity
One of the biggest challenges is ensuring that the existing building can support the additional weight of the mezzanine. Mezzanine floors add significant load, so it’s crucial to evaluate the building’s ability to handle this extra weight. A thorough site assessment is necessary to check the strength of the current structure. This includes working with structural engineers to perform load-bearing calculations and ensure the building’s foundation and frame are adequate.
Design Constraints
Fitting a mezzanine into an existing space requires careful design. Mezzanines must be integrated into the current layout while meeting functionality needs. This often involves customising the design to fit around existing columns, beams or equipment. Balancing practical needs with aesthetic considerations can be challenging but is essential for creating a usable and visually appealing space.
Regulatory Compliance
Complying with building codes and safety regulations is a key part of the installation process. Different regions have specific rules for mezzanines, including fire safety and accessibility requirements. Securing the necessary permits and approvals is essential to avoid legal issues. Make sure to understand local regulations and work with professionals who can help navigate these requirements.

Pre-Installation Planning
Site Analysis
Before starting the installation, a detailed site analysis is crucial. This involves surveying the space to identify any potential obstacles or hazards. Understanding the layout and existing infrastructure will help in planning the mezzanine installation effectively. This step ensures that any issues are addressed early on, preventing delays and complications later.
Load-Bearing Calculations
Calculating how much weight the mezzanine floor will need to support is essential. This includes the weight of the mezzanine itself, plus any equipment, materials, and personnel that will be on it. Accurate load-bearing calculations are necessary to ensure the safety and stability of the mezzanine. Structural engineers can help with these calculations to make sure the design meets all requirements.
Design and Layout
Customising the mezzanine design to fit the specific needs of the business is important. The design should make the best use of available space and integrate seamlessly with existing infrastructure. Considerations like the placement of support columns, flooring type, and access points are important. The design should also account for future needs, allowing for possible expansion or modification.
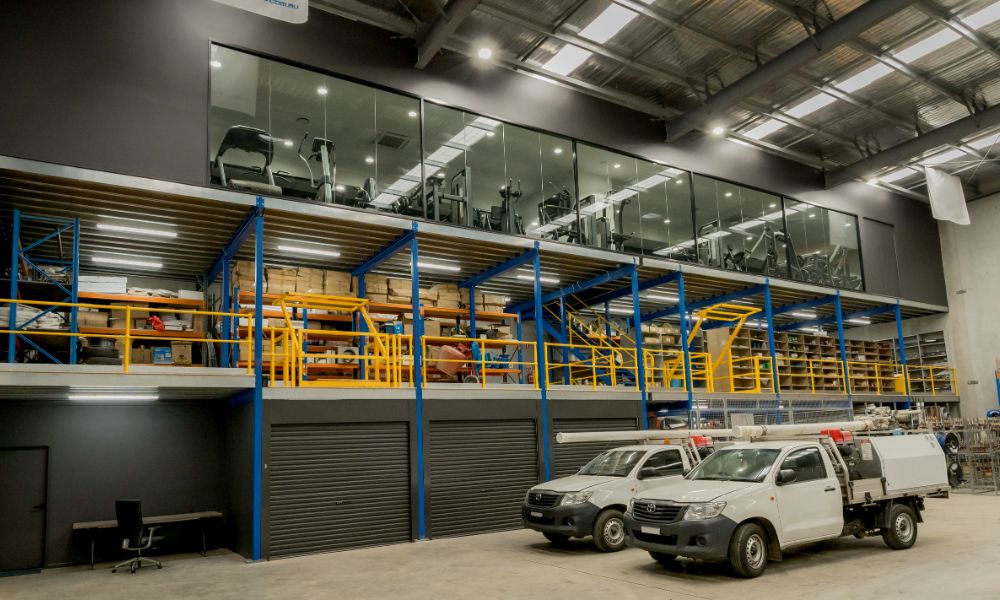
Material Selection and Procurement
Choosing the Right Materials
Selecting the right materials for the mezzanine floor is crucial for its durability and functionality. Factors to consider include strength, durability, and cost. Common materials include steel, which is strong and durable, and other options like wood or composite materials depending on the application.
Procurement Challenges
Managing the procurement of materials can be challenging, especially with potential supply chain issues or delays. It’s important to work closely with suppliers to ensure timely delivery of materials. Having a clear plan and contingency options can help address any procurement challenges and keep the installation on track.
Installation Process and Techniques
Foundation and Support
Preparing the foundation for the mezzanine is a critical step. This involves reinforcing the existing floor and installing support columns and beams. The foundation must be strong enough to support the mezzanine and the additional load. Proper preparation ensures the stability and safety of the mezzanine.
Assembly
Assembling the mezzanine involves careful precision and alignment. This includes installing the flooring, handrails, and access points. A step-by-step approach helps ensure that all components are correctly assembled and aligned. This attention to detail is important for maintaining the structural integrity and functionality of the mezzanine.
Safety Measures
Implementing safety protocols during the installation process is essential. This includes using appropriate safety equipment and training workers on safe installation practices. Regular inspections of the worksite for potential hazards help ensure a safe working environment and compliance with safety regulations.
Overcoming Specific Installation Challenges
Limited Space and Accessibility
Installing a mezzanine in a confined space can be challenging. Solutions such as using modular and prefabricated components can help. Modular systems are easier to handle and assemble in tight spaces, making them suitable for installations with limited accessibility.
Integration with Existing Structures
Integrating the mezzanine with existing structures requires careful planning. This includes ensuring that the mezzanine aligns well with existing utilities, fixtures, and access points. Addressing these integration challenges is crucial for a seamless installation that works well with the current facilities.
Unexpected Issues
Unexpected challenges can arise during installation, even with thorough planning. Having contingency plans in place and being ready to adapt to changes can help manage these issues. Flexibility and a proactive approach can help address unforeseen problems effectively.
Post-Installation Considerations
Inspection and Quality Assurance
After installation, conducting a thorough inspection is important to ensure the mezzanine meets all safety and quality standards. Any issues or deficiencies should be addressed promptly to maintain the mezzanine’s integrity.
Maintenance and Upkeep
Regular maintenance is key to ensuring the mezzanine’s longevity and safety. This includes routine inspections and addressing any signs of wear and tear. Proper upkeep helps maintain the mezzanine’s structural integrity and functionality.
Feedback and Improvements
Gathering feedback from users can provide valuable insights into the mezzanine’s performance. This feedback can be used to make necessary adjustments and improvements, ensuring the mezzanine continues to meet the business’s needs effectively.
Mezzanine floor systems are a practical way to maximise space, but their installation can involve several challenges. By understanding and addressing these challenges, businesses can ensure a successful installation that enhances their operational efficiency. Thorough planning, careful material selection, and adherence to best practices are crucial for overcoming the complexities of mezzanine floor installation. Seeking professional assistance and expertise can further support a smooth and effective installation process. If you’re ready to explore how mezzanine flooring can help grow your business, contact Adex today.